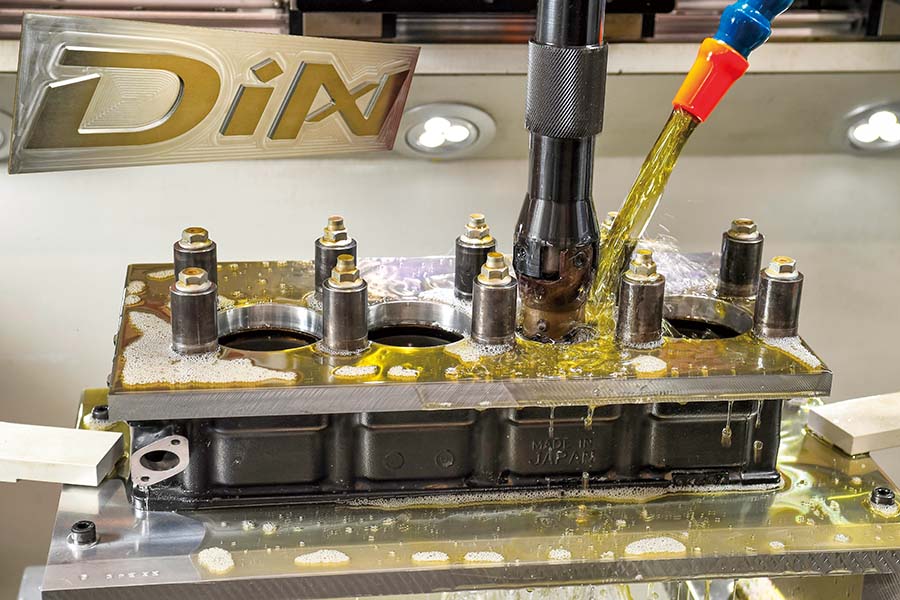
組み手やチューナーの狙いを助けニンジャの寿命や性能を高める内燃機加工・DiNx(ディンクス)
ニンジャならではのシリンダー水圧検査
アイキャッチの写真は、GPZ900Rシリンダーのホーニングを始めるところだ。ダミーヘッドプレートを組み、位置決めして必要な切削量を入力する。それに合わせてツール(シリンダーに入る黒い棒。シリンダーに入る部分に刃が付く)が回転し、加工される。
▲バルブシートカットの作業イメージ写真。1カ所につき30/45/60度の3段を1度に加工できる。
上の写真は同じくGPZ900Rの、シリンダーヘッド。バルブガイドを打ち替えた後にバルブシートカットを行っている様子だ。このような、オーバーホールやチューニングなどエンジンを分解し、組み立てる時に必要な加工がいわゆる内燃機加工。そしてDiNx(ディンクス)は2/4輪エンジンに対してその内燃機加工を請け負う会社だ。
今回ちょうどGPZ900Rエンジン各部が作業を受け、納品される状態にあったので、具体的にどんな加工がされているかを順に追ってみた。ところで、ニンジャだからという部分はあるのだろうか。
▲作業を終え納品状態のGPZ900R用シリンダー。合わせ面は面研され滑らかで艶やかな仕上がり。シリンダー内壁もきれい。
「対象物、つまりシリンダーやクランクシャフト、シリンダーヘッドなどを、求められる数値に加工するのが当社の仕事になります。GPZ900Rの場合でもいわゆるエンジンの加工ですから作業内容自体は他モデルのエンジンと基本的には同じです。ただウエットライナー式のシリンダーですから、入ってきた時の確認で水圧検査という作業が入ります」とのこと。
ニンジャエンジンの特徴とも言えるウエットライナー。シリンダーブロックに鋳鉄製スリーブを組むという点では他の同世代エンジンと変わらないが、ニンジャは熱交換性を高めるためにスリーブの外に直接冷却水が触れるようになっている。そのスリーブ下側とシリンダーブロックの間には冷却水漏れを防ぐOリングが入るが、この劣化や切れなどがあるとエンジン内に水が浸入してしまう。
▲こちらも作業を終えた納品状態のGPZ900R用シリンダーヘッド。バルブガイド打ち替えやシートカット等が施されている。
そんな漏れがないか、冷却水を水路に満たし、運転時にかかる圧力も想定した数値でかけて確認するのが「水圧検査」だ。DiNxでは依頼があればボーリング前(ライナー入れ替えの時は入れ替え後)にこの作業を行う。
組み手の望む状態に正しく加工していく
ここからは各作業だ。前回秋に訪れた時(その時の記事はこちら)は涼しかった社内は、今回は少し暖かめ。作業環境が通年で20℃に保たれているからだ。用意されたパーツに対する作業は、どれも測定から始まる。
▲まずはすべての作業の基本となる各部の測定からだ。
「シリンダーなら各気筒の内径を計ります。X(横)とY(縦)、それを上、中、下で。測定はすべての基本ですから、作業後にも同様に計り、いただいた寸法で仕上がっているかを確認する。
加工寸法は使うピストンやそれに対するクリアランスも考えてショップさんなどお客さんが指定する値です。私たちはそれを高精度に合わせます。使い方や機種などによる違いやそれに対するノウハウはありますが、それは加工上のもので、組み手さんは自身の考えでクリアランスを狭く取るなどの数値を決めて依頼される。それを正しく反映するようにしています」
同じ径のピストンを使うにしても、同じ数字でボーリングするわけではない。組み手が狙う、回り方やパワーの出方などの仕様で細かく変わる。それは組み手が考え、指定する。受ける加工側ではその数値を正しく出し、狙う数値を実現することで応えていく。
▲切削加工機(YZ500-WR)にシリンダーを水平にセットし垂直にボーリング作業を行う。作業開始でツールが回転し先端の刃で切削する。
シリンダーは切削加工機(ここではYZ500-WR)で内径を拡大するボーリングを行う。水平を出してシリンダーの芯を出し、シリンダー(ピストン)中心位置から狙う外径分に合わせて、垂直方向に上下しながら回転するツールに付いた刃で順序よく内壁を切削する。この時点で次のホーニング用取りしろ(仕上げしろ)は1/1000mm台だ。
▲ダミーヘッドプレートがセットされ専用のコンピュータ制御ホーニングマシン(ロッテラーH85A)でオイル保持溝を刻みつつ仕上げる。
4気筒分を削ると仕上げのホーニングに移る。エンジンを組んだ時同様の環境になるようにダミーヘッドプレートを組み、専用のコンピュータ制御ホーニングマシン(ロッテラーH85A)にボーリング時と同様に位置決めし、仕上げ切削を行う。残った取りしろを削ると同時にその外(内壁表面)にはクロスハッチ(オイル保持用の溝)を切っていく。DiNxでは高原状の表面に深めの溝を掘るプラトーホーニングを基本とする。
これが済むとシリンダー上面を平滑に仕上げる面研などの作業を行って納品となる。
「排気量拡大や長年使ったなどでスリーブを打ち替える場合もあります。その場合はシリンダー下側のOリング溝も掃除しOリングも新品交換。スリーブは圧入となりますが、この時にOリングのねじれや切れがないように入れていきます。そのあとの加工は同じで、ともにすぐ使える状態で納めます。
ただ、水圧検査で漏れが見つかった場合はすべてやり直しになります。スリーブは当然入れ替え、改めてボーリング、ホーニングという手順を経ることになります。ほとんどないことですけど、それも見越して検査して作業しているとご理解いただければいいですね」
荒れや変形を見つけ出し正しい状態を作る作業
シリンダーヘッドは工程の多い箇所だ。燃焼室やポートの加工は組み手やチューナーが個別に腕を振るう部分(内燃機加工業で行う場合もある)として、きちんとした吸気/燃焼/排気ができるよう、燃焼圧を正しく捉えられるようにしていく。そのためにバルブを支えるバルブガイドの内径が広がったり変形、穴が斜めになったりしていないかを確認する。
▲シリンダーヘッドからバルブガイドを抜き、ライトを当てて目視で傷や荒れの有無を確認。
NGならばガイドを抜き、ガイド穴(下穴)を確認。荒れはないか、まっすぐか。もちろん新しいガイドに合う径かも計り、16個のガイドが緩いきつい(どちらも不具合が出る)がないようにして入れる。荒れの傷はオイル漏れにつながるから面を慣らし、ヘッド全体を均一に暖めて新しいガイドをまっすぐ入れる。新しいガイドは内径を計り、使うバルブとのクリアランスを確認し、仕上げる。
バルブが決まれば次は燃焼室側。カーボンの噛み込みや使用にともなう変形を戻し、バルブフェイスがシートに密着するようにバルブシートカットを行う。ヘッド加工ツール(ミラHM2000エボ)にヘッドを載せ、シートカッター(同軸のガイドをバルブガイド穴センターに入れる)で30度/45度/60度の3段を1回でカットする(オーダーにも応じる)。これらの作業ができたら下面を面研して仕上げ、納品へ移る。
▲鍛造一体成形のニンジャクランク。クランクのスムーズな回転を実現するには、スタティック(静的)なバランスはもちろん、回転させてのダイナミックバランスの確認も大切。
またニンジャでは鍛造一体成形のクランクも、回転状態で見るダイナミックバランスを取る。
「スタティック(静的)で取る分に加えてダイナミックだと軸芯からどのウエブのどの角度が重いか分かるので、その部分を落としてゼロに近くできます。ジャーナルラッピングも合わせてできます」
DiNxによれば、各部分の劣化や摩耗、傷みは数字に出るとのこと。それをきれいにする、外れた数字をあるべき数字に戻す。ノーマルの持っているレベル=ゼロ状態を再現しながら、組み手が狙うスペックを引き出せるように、指示された数値を高い精度(1/1000mm台)で加工できること。
「当たり前のこと(ここでは内燃機加工)を当たり前にやるだけですよ」とのことだが、その当たり前がエンジンの調子を戻す。いや、もっと良くしてくれる。ニンジャもそうできるのだ。こんな加工の話が出てきたら、ここに紹介したような内容も思い出してほしい。
シリンダーは測定&水圧検査後にボーリング&ホーニング、面研して納品
GPZ900Rシリンダーの内燃機加工では、スリーブ劣化からの復帰や大径ピストン使用などの必要に応じてシリンダースリーブの打ち替えが加わる。作業は一貫して20℃の環境下で行われる。スリーブ内径測定(横方向/縦方向を上/中/下で計る)と水圧検査後に指定近くまで内径を拡大するボーリング。オイル保持溝を刻みつつ仕上げるホーニングと続き、面研も行い納品となる。
【各部測定】
【水圧検査】
GPZ900Rシリンダー加工前の確認作業として行われる水圧検査。シリンダーブロック上下面のウォーターホールを塞ぐようにゴム板を挟んでアルミプレートで留め、冷却水を満たした上でハンドポンプで0.2MPa(2kgf・m/cm2近く)程度の圧力をかける。Oリング劣化などがあればシリンダーブロックとスリーブの境目に冷却水がにじみ出てくる。
【ボーリング】
セットと芯出しの後に作業が行われる。作業後の振れ等の測定も重要。
【ホーニング】
【作業後のシリンダー】
仕上がったシリンダー。内壁にはX字状に交差するような細かい溝=クロスハッチが刻まれているのが分かる。オイル保持用でこれは使用にともなってなめらかになっていく。ここでもリフレッシュが図られる。上面も面研され、新品以上になめらかだ。
バルブ&バルブガイド/シート加工などが集中するヘッドまわり
まずは、シリンダーヘッドからバルブガイドを抜いた状態にする。
ガイドを抜いた穴(下穴)はカム側/燃焼室側(写真)から光を当てて目視し、傷や荒れがあれば修正(ひどければフライス盤加工も)する。
目視の結果、今回は状態は良好だった。
ガイド穴の内径を計測する。
使用するバルブガイドの外径も計る。
下穴の内径に合うバルブガイドを選んだ上で電気炉でヘッドを120℃近辺に均一に暖めてガイドを圧入する。他の熱し方では熱の入り方(膨張率)が均一でないままきついガイドが入ってしまい、ガイドが膨張してヘッド割れを招くこともありうる。
新しく入れたバルブガイド(写真上)はバルブの入る穴の内径を計り、同じくバルブステムも外径を計る(写真下)。両者が適正クリアランスになるように必要に応じてリーマーで内径を合わせる。このあたりも計測に次ぐ計測という感じで作業が進められていく。
バルブガイドの処理がすんだらバルブフェイスに合わせてバルブシートカット処理。
ツール先端のガイドセンターがバルブガイドセンターに合うようにセットし、シートカットする。
30/45/60度の3段が一度に処理できる。フェイス当たり面幅や角度、ビッグバルブなどでの加工は指定に応じて行う。
クランクシャフトはダイナミックバランスを取る
鍛造一体成形のGPZ900Rクランクの回転のスムーズ化を図るべくバランスを取るが、DiNxではダイナミックバランスも取る。バランサーにクランクを載せて回転させるとどのウエブのどの角度が重い(バランスがずれて偏った回転をしている)かが分かる。
Vブロックに載せて指定ウエブの重量を落としてバランスをゼロに近づける。軽量加工やジャーナルラッピングも可能だ。
【協力】
DiNx(ディンクス) TEL04-7157-2091 〒277-0902千葉県柏市大井554-6 https://DiNx.co.jp
※本企画はHeritage&Legends 2023年4月号に掲載された記事を再編集したものです。
バックナンバーの購入は、https://handlmag.official.ec/ で!
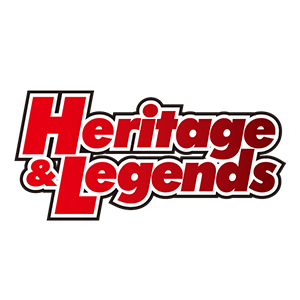
WRITER